Ferrous/Non-ferrous
Product Name: Pall Rings
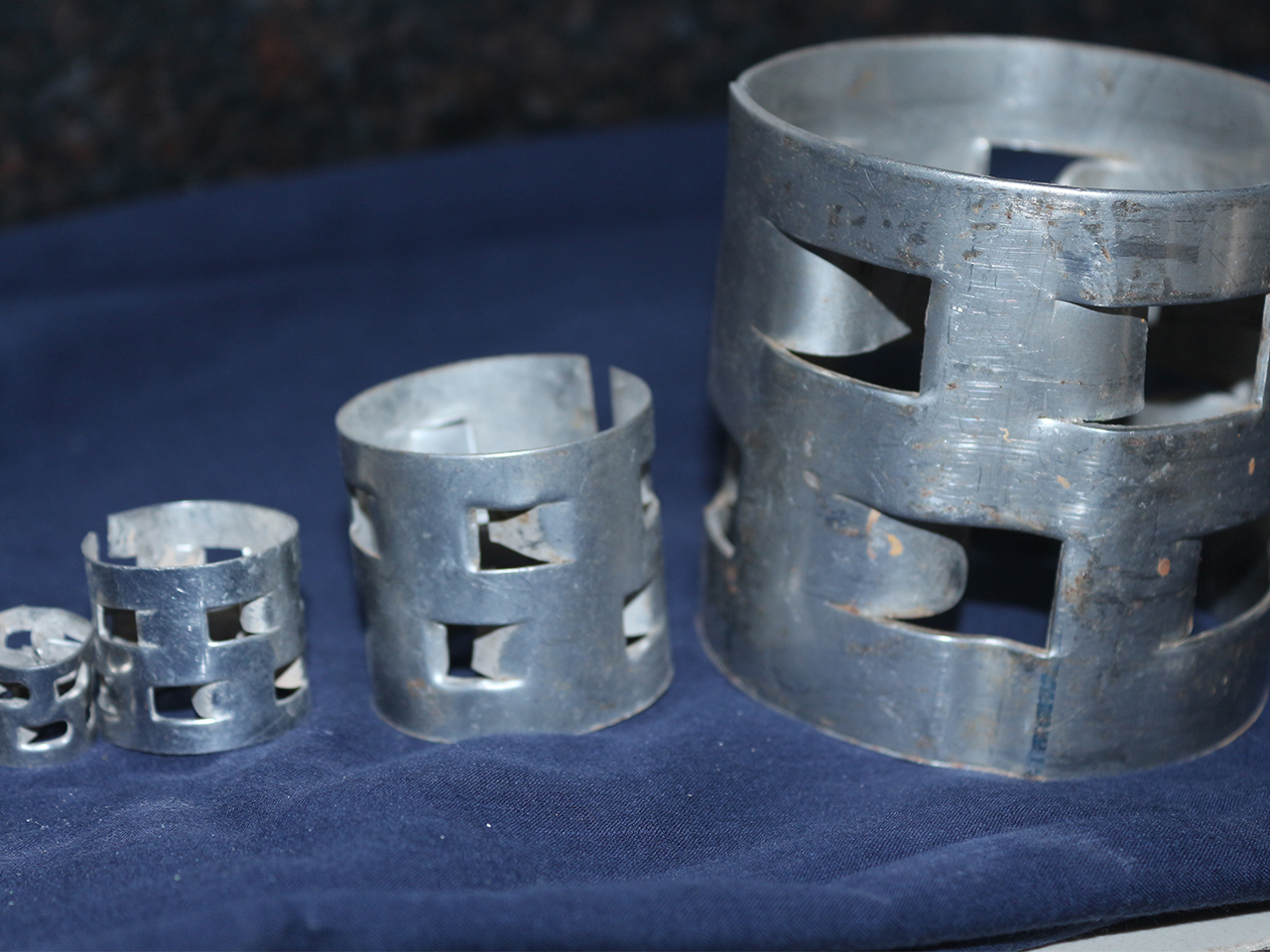
Specification
Guage | No. of pieces per M^3 +10% | Wt. Per M^3 in Kgs +10% | Surface area M^2/M^3+10% | % Free space | |
---|---|---|---|---|---|
12mm | 22 | 370968 | 1393 | 488 | 72 |
12mm | 24 | 374251 | 1092 | 491 | 73 |
12mm | 26 | 377534 | 878 | 495 | 74 |
15mm | 22 | 233510 | 1378 | 483 | 76 |
15mm | 24 | 234746 | 1076 | 485 | 78 |
15mm | 26 | 235981 | 865 | 488 | 79 |
20mm | 22 | 107436 | 1128 | 392 | 77 |
20mm | 24 | 108336 | 881 | 396 | 78 |
20mm | 26 | 109236 | 707 | 399 | 79 |
25mm | 22 | 45325 | 740 | 258 | 84 |
25mm | 24 | 45713 | 580 | 261 | 85 |
25mm | 26 | 46101 | 466 | 263 | 86 |
35mm | 22 | 14120 | 452 | 158 | 90 |
35mm | 24 | 14226 | 354 | 159 | 91 |
35mm | 26 | 13908 | 692 | 156 | 92 |
50mm | 22 | 5930 | 602 | 135 | 93 |
50mm | 24 | 6036 | 394 | 138 | 94 |
50mm | 26 | 6070 | 490 | 139 | 94 |
Product Name: RASCHIG RINGS

Specification
Guage | No. of pieces per M^3 +10% | Wt. Per M^3 in Kgs +10% | Surface area M^2/M^3+10% | % Free space | |
---|---|---|---|---|---|
12mm | 22 | 398890 | 1135 | 397 | 77 |
12mm | 24 | 402420 | 891 | 400 | 78 |
12mm | 26 | 405950 | 716 | 404 | 79 |
15mm | 22 | 251423 | 1110 | 392 | 80 |
15mm | 24 | 252747 | 879 | 395 | 80 |
15mm | 26 | 254071 | 704 | 397 | 80 |
20mm | 22 | 115519 | 917 | 320 | 82 |
20mm | 24 | 116490 | 719 | 323 | 82 |
20mm | 26 | 117461 | 577 | 326 | 83 |
25mm | 22 | 48749 | 600 | 210 | 86 |
25mm | 24 | 49173 | 472 | 212 | 86 |
25mm | 26 | 49597 | 379 | 214 | 87 |
35mm | 22 | 14826 | 557 | 125 | 90 |
35mm | 24 | 15037 | 365 | 128 | 92 |
35mm | 26 | 15143 | 286 | 128 | 93 |
50mm | 22 | 6534 | 489 | 113 | 92 |
50mm | 24 | 6612 | 323 | 114 | 93 |
50mm | 26 | 6647 | 256 | 115 | 93 |
75mm | 28 | 1871 | 325 | 73 | 95 |
SERVICE APPLICATION
Material of Construction | General Service Application | Limiting Factors |
---|---|---|
Ceramic | Neutral and acid condition | Fluorine compound, Hot caustic above 70 degree F. |
Plastic | Alkali, Salts and acids depending on choice or resin | Temperature, Higher initial cost. |
Metals | Hot alkalies, acids, depending on metal. | Highly corrosive environment, Higher Initial cost. |
Carbon | Hot Alkalies | Temperature >100C |
Packing Procedures
The packing is supported on a grid or screen which must be of an open pattern which does not offer a high resistance to flow. If the tower is high, redistribution plates are necessary. These plates are needed at intervals of 2.5 – 3 column diameters for Raschig Rings and 5 – 10 columns diameters for Pall Rings, but are usually not more than 20 feet apart. A hold down plate is often placed at the top of a packed column to minimise movement and breakage of packing caused by surges in flow rate.
Ring Packings are either dumped into a water filled tower to reduce breakage, or may be individually stacked if 3″ in size of larger. To obtain high and uniform voidage and to prevent breakage it is often found better to dump the packings into a tower full of liquid. Saddles are dumped.
While filling in the dry state the packing is carefully poured down the walls of the columns so that a concave surface is formed; when the surface is sufficiently hollowed this hollow is largely filled in by the introduction of the packing in a number of small heaps adjoining each other. After each series of heaps is formed they are flattened and a further series of small heaps is formed and so on until the hollow which is filled in as before. Packing in such manner will partially control the tendancy of the liquid to migrate to the wall. Alternatively unevenly dimensioned packings can be used.
A tower designed with the above points in mind utilizing modern packings, tower internals and proper packing methods would achieve near theoretical performance.